日本には数多くの縫製工場があります。その中で、オーダースーツを年間1万着以上を縫製するのが約60社。株式会社ジェンツはその60社の中の、3社の三ツ星認定工場(2016年2月、IACDEより)の1社である。今回はそのジェンツの話。
TAILORS WORLD編集部の山本佑です。
株式会社ジェンツの創業は、昭和44年8月6日で、現在は福島県福島市と埼玉県春日部市の2工場で製造しています。福島工場は従業員110名で主に、紳士物の上着とベストの生産しており、春日部工場は、従業員25名で紳士物のズボンの生産をしています。
そのジェンツの強みとして1つ目は、紳士服を製造するためのコンピュータシステムです。現場が作業しやすくするためのコンピュータシステムを自社で独自に開発し、使用しています。また、裁断は、最新のCAM(製品製造・加工システム)を2台導入し、裁断効率を高めています。
2つ目は、職人の手による卓越した技術です。 裁断する際、機械で裁断できない場合は、人の手で一点一点手裁断しています。
そんな強みあるジェンツ。その工場の現場をご紹介させて頂きます。
圧倒的な広さの工場内
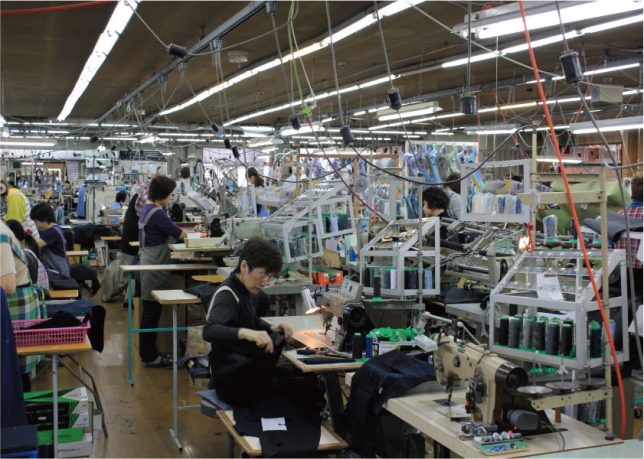
1000平方メートル以上の広大なフロアで職人約130人が作業しています。また、あらゆるお客様の縫製にお応えするために日々職人の方々は、スピード、生産率を上げるため黙々と作業をしています。
データー入力
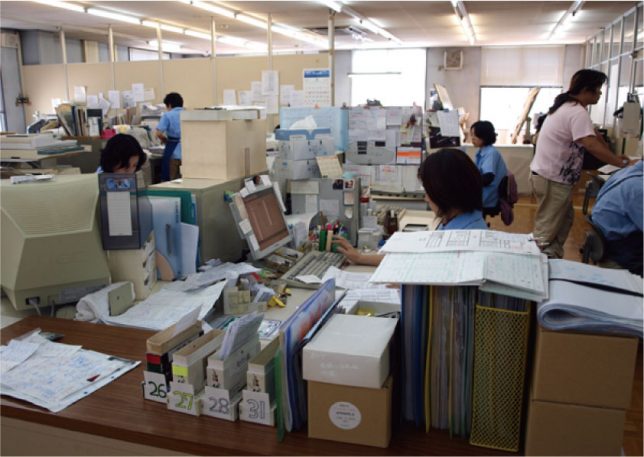
お客様の寸法やデザインが記入されたオーダーシートを1枚ずつチェックし、データ入力していきます。
受け付けた注文はまず工場内のコントロールセンターで管理番号が付与され、納期など情報を元にサイクルが決定されます。その受け付け伝票は、約6人の方々で厳密に管理され、毎日オーダーが到着します。
間違いない様、2重、3重チェックを行いながら、オーダーシートの漏れ等を防ぐ役割を果たしています。
生地のチェック
お客様からお預かりした生地を、地のしを行います。裁ち台に広げ、キズ汚れのチェックをしながら、ストライプやチェックの柄が合う様に折りたたみます。
CAD/CAM&手裁断
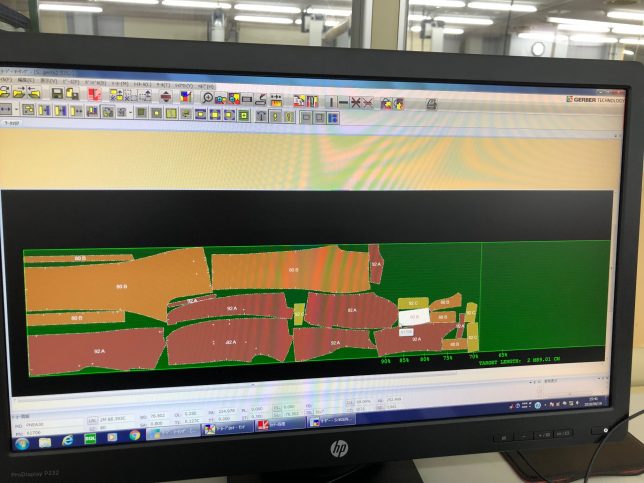
最初に入力したデータの型紙が作成され、型入れを行います。
ジェンツは高級紳士服を謳ってますので基本的には一方方向での裁断が原則です。原則一方裁断ですが、キズを自動的に避け差込みを配列する技術も採用しています。
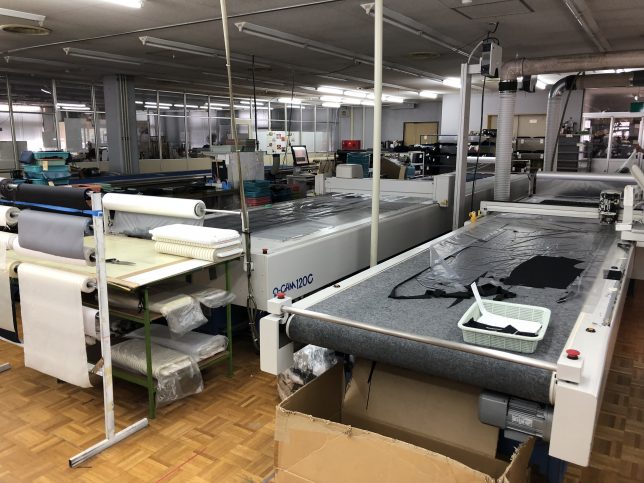
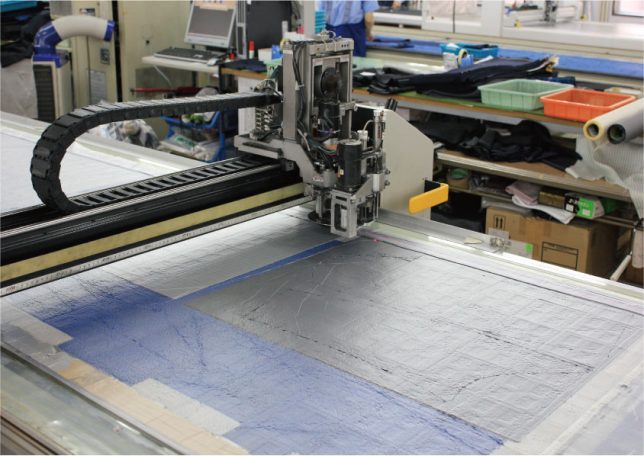
型入れしたデータでCAMにて自動裁断を行います。
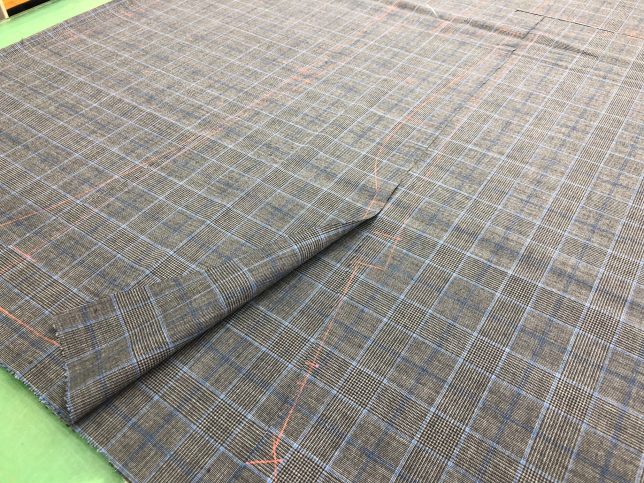
格子柄の生地や特別な裁断が必要なものなどは、熟練の職人が持つ優れた技術をおろそかにせず、柄合わせをし一つ一つのパーツを1着ずつ丁寧に手裁断を行います。
縫製前準備
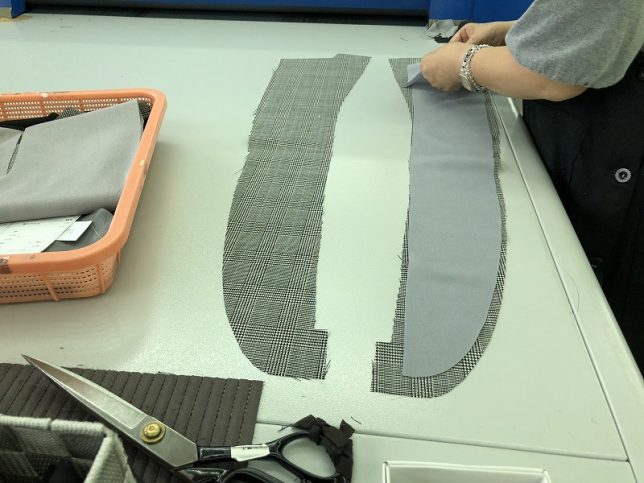
裁断後のパターンに芯を貼ったり、ポケットの袋地を集めたり、縫製前の準備が行われ、縫製工程に入っていきます。
縫製
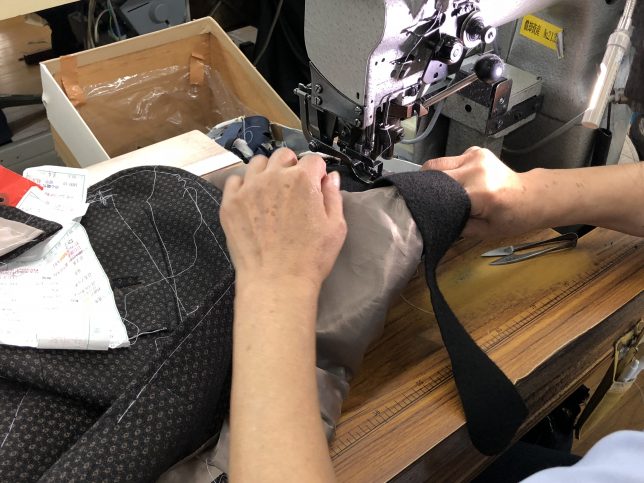
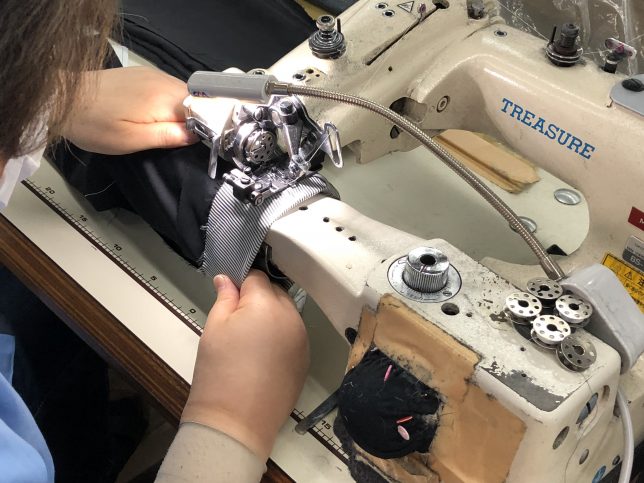
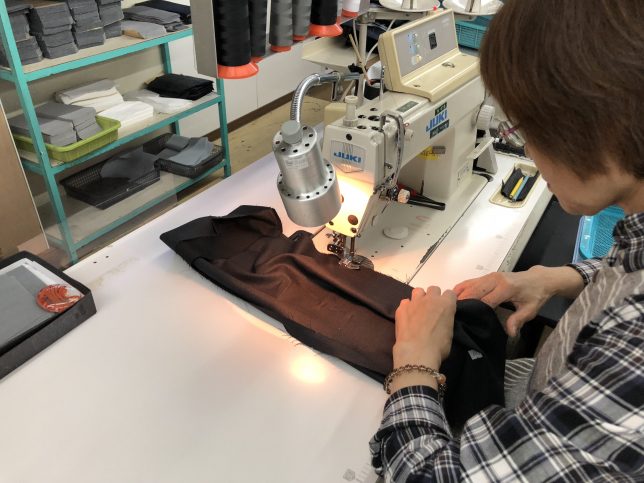
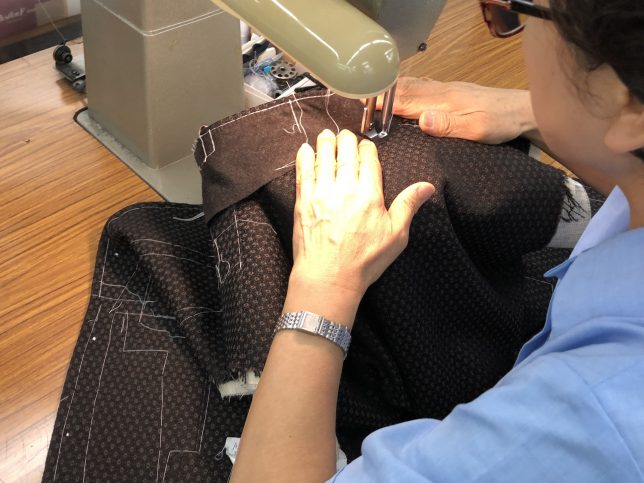
縫製は300工程位あります。縫製工程は、各パーツごとにチームに別れ、流れ作業で効率よく並べられた最新鋭ミシンで熟練の技と高性能の機械が力を合わせることにより、完成度の高いスーツが生み出されています。
ミシンだけでも、ボタンホールミシン、芯据えミシン、ハ刺しミシン、袖付ミシン、まつりミシン、ポケットマシーン、ピンポンミシン等、見返し、後ろ身頃、衿、袖、前身頃がそれぞれのパーツで縫製され、1着のジャケットに組み立てられていきます。各工程毎に中間プレスや中間検品を行い、この世に1着の商品が出来上がっていきます。
縫製後検品
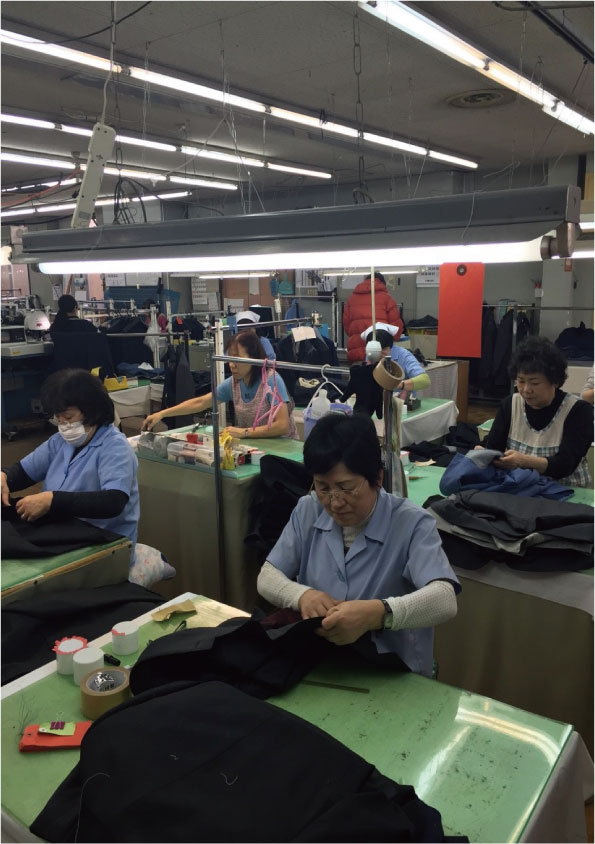
全縫製工程が終わった後の最終チェックがあります。オーダー項目伝票が仕上がった製品に付いており、仕様、糸ホツレ等、細かく6人体制で検品をしています。
仕上げ
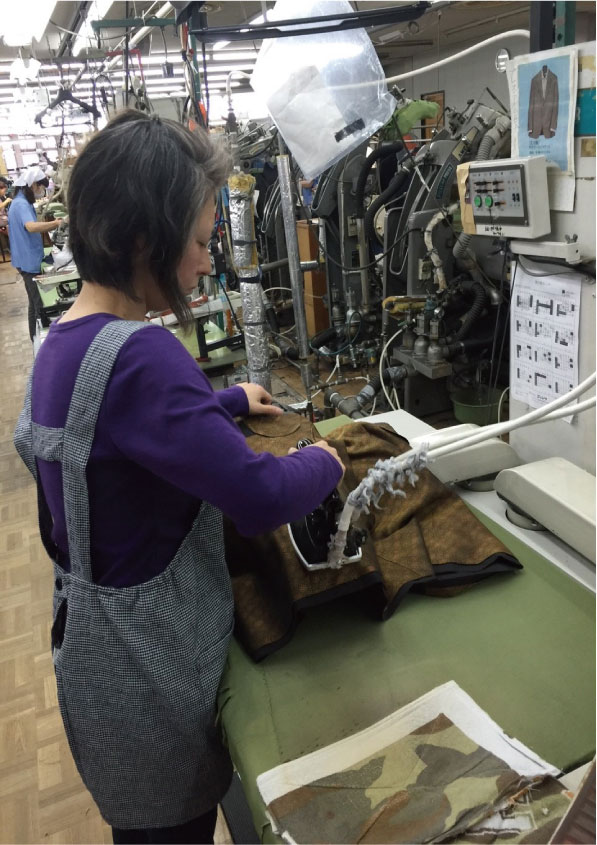
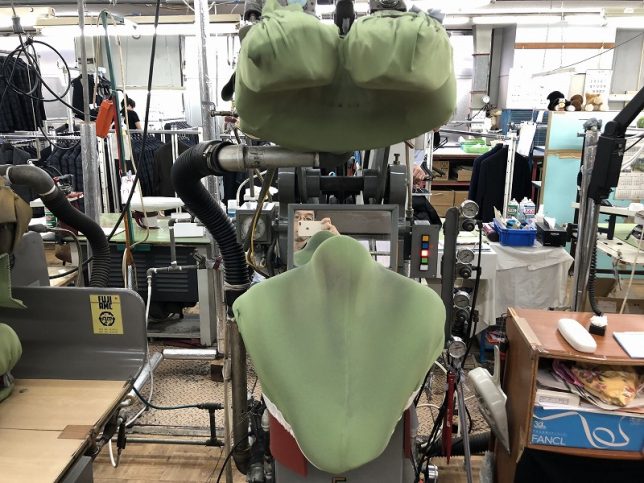
縫製検品を経て、身頃、袖、肩、衿、各部に専用のプレス機と職人を配置します。更に、プレス機を終えた後人の手でプレス作業をします。最後まで妥協を許しません。プレス後は、立体的なジャケットが出来上がります。
最終検品
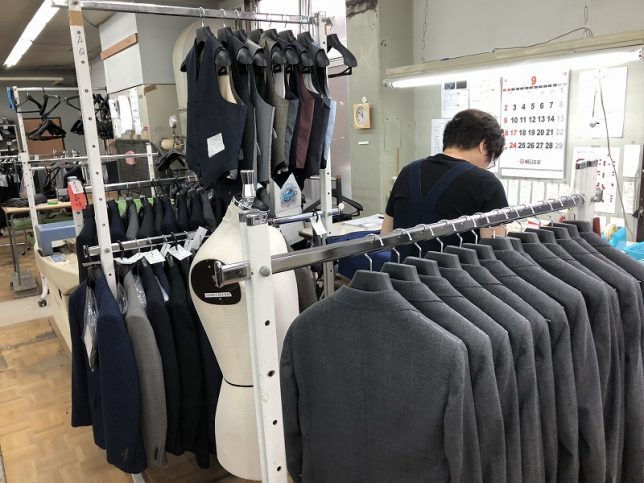
最終検品と検針を行い無事出荷となります。
スーツ1着を作り上げるのに、様々な工程を経て、たくさんの人の手を加え、出来上がるのだと改めて感じました。
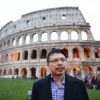
全国展開のオーダースーツ店にて2年間修行後、服飾資材の道に。
特にスーツ(重衣料)の事ならお任せください。